Australische Wissenschaftler stellen 3D-gedruckten Kunststoff her, der mit einem dem Harz hinzugefügten “Spezialpulver” hergestellt wird, das sich selbst heilen kann, wenn es unter LED-Licht gesetzt wird
- Wissenschaftler haben einen selbstheilenden Kunststoff entwickelt, der im 3D-Druck verwendet werden kann
- Dem im Druckprozess verwendeten flüssigen Harz wird ein spezielles Pulver zugesetzt, das bei der Reparatur von Materialien hilft, wenn sie beschädigt werden
- Die Reparaturen können bei Raumtemperatur durchgeführt werden und müssen nur unter LED-Beleuchtung erfolgen
Ein Team von Wissenschaftlern der University of New South Wales (UNSW) hat einen Weg aufgezeigt, wie 3D-gedruckter Kunststoff schnell und kostengünstig „selbstheilend“ werden kann, was einen großen kommerziellen Durchbruch bedeutet.
Das Team fand heraus, dass das Hinzufügen eines speziellen Pulvers zum flüssigen Harz, das beim Druckprozess verwendet wird, bei der Reparatur von Materialien helfen kann, falls sie beschädigt werden.
Die Reparaturen können bei Raumtemperatur durchgeführt werden und müssen nur unter LED-Beleuchtung erfolgen, die eine chemische Reaktion und das Verschmelzen der Bruchstücke auslöst.
Um das gleiche Ergebnis zu erzielen, müssen die Produkte derzeit möglicherweise zerlegt und die defekten Komponenten einer Reihe von Heizzyklen unterzogen werden.
Es dauert auch ungefähr 24 Stunden im Vergleich zu einer Stunde mit der neuen Methode.
Das Team fand heraus, dass das Hinzufügen eines speziellen Pulvers zum flüssigen Harz, das beim Druckprozess verwendet wird, bei der Reparatur von Materialien helfen kann, falls sie beschädigt werden. Die Reparaturen können bei Raumtemperatur durchgeführt werden und müssen nur unter LED-Beleuchtung erfolgen, die eine chemische Reaktion und das Verschmelzen der Bruchstücke auslöst
Während dreidimensionaler Druck oder additive Fertigung im Allgemeinen weniger Umweltbelastungen verursachen, entspricht es noch nicht der strengen Definition von Umweltfreundlichkeit.
Da viel Plastik im Spiel ist und Drucker tagelang laufen, ist jede Verzögerung durch die Reparatur von Bruchstücken traditionell mit zusätzlicher Zeit, Geld und Abfall verbunden, sagt der Sprecher des Forschungsteams, Dr. Nathaniel Corrigan.
Aber jetzt lassen sie sich einfach und schnell reparieren, und in vielen Situationen können auch beschädigte Bauteile geborgen werden, anstatt sie für einen Neustart wegzuwerfen.
“Es gibt einen offensichtlichen Vorteil für die Umwelt, da Sie nicht jedes Mal ein brandneues Material neu synthetisieren müssen, wenn es kaputt geht”, sagte Corrigan.
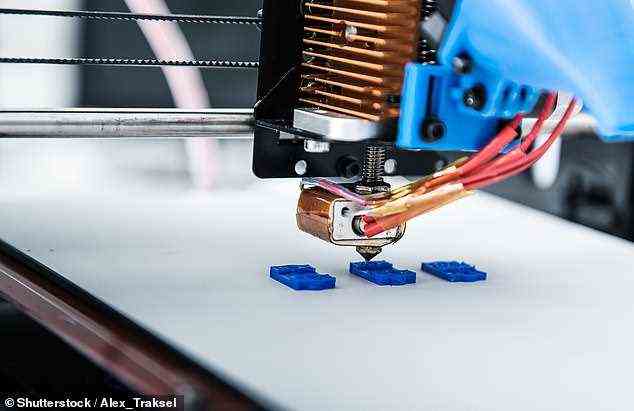
Das verwendete pulverförmige Additiv ist ein ursprünglich vom CSIRO entwickeltes Trithiocarbonat- oder RAFT-Mittel. Trithiocarbonat wird aus der Reaktion von Hydrogensulfid mit Schwefelkohlenstoff gewonnen. Es ermöglicht die Neuordnung des Netzwerks der Elemente, aus denen das gedruckte Material besteht, und ermöglicht deren Verschmelzung
“Wir verlängern die Lebensdauer dieser Materialien, wodurch Plastikmüll reduziert wird.”
Das verwendete pulverförmige Additiv ist ein ursprünglich vom CSIRO entwickeltes Trithiocarbonat- oder RAFT-Mittel.
Trithiocarbonat wird aus der Reaktion von Hydrogensulfid mit Schwefelkohlenstoff gewonnen.
Es ermöglicht eine Neuordnung des Netzwerks von Elementen, aus denen das gedruckte Material besteht, und ermöglicht deren Verschmelzung.
Dies geschieht innerhalb von etwa 30 Minuten, wenn UV-LED-Lichter direkt auf den gebrochenen Kunststoff gestrahlt werden, wobei die vollständige „Heilung“ in etwa einer Stunde stattfindet.
Experimente, unter anderem an einer 3D-gedruckten Geige, zeigen, dass die Festigkeit des selbstreparierten Kunststoffs vollständig in seinen ursprünglichen, ungebrochenen Zustand zurückversetzt ist.
Das Team glaubt, dass eine Kommerzialisierung aufgrund der Vereinfachung und Geschwindigkeit ihres Systems möglich ist.
“Es gibt andere Verfahren, die dies tun, aber sie basieren auf der thermischen Chemie, um das Material zu reparieren, und normalerweise dauert es etwa 24 Stunden und mehrere Heizzyklen, um das gleiche Ergebnis zu erzielen”, sagte Corrigan.
„Eine weitere Einschränkung besteht darin, dass Sie einen auf hohe Temperaturen erhitzten Ofen benötigen und das Kunststoffmaterial offensichtlich nicht vor Ort reparieren können – Sie müssten es zuerst vom Bauteil demontieren, was zu einer höheren Komplexität und Verzögerung führt.
„Mit unserem System können Sie den gebrochenen Kunststoff an Ort und Stelle belassen und das gesamte Bauteil mit Licht beleuchten.
“An vielen Stellen, an denen ein Polymermaterial verwendet wird, können Sie diese Technologie verwenden”, sagte er.
Corrigan und die UNSW-Kollegen Cyrille Boyer und Michael Zhang glauben, dass die Technologie in einer Reihe von Anwendungen eingesetzt werden könnte, bei denen fortschrittliche 3D-Materialien in spezialisierten Hightech-Komponenten verwendet werden.
Dazu gehören tragbare Elektronik, Sensoren und sogar einige Schuhhersteller.