Tische und Stühle, die sich aus 3D-gedrucktem Holz selbst zusammenbauen, könnten dem Albtraum ein Ende bereiten, Möbel zusammenzubauen.
Wissenschaftler in Israel haben eine druckbare „Holztinte“ entwickelt, die so programmiert werden kann, dass sie sich beim Trocknen in komplexe Formen wie Kuppeln, Spiralen und sogar Pringle-Formen verwandelt.
Die Experten haben bisher Designs gedruckt, die nur wenige Zentimeter lang sind, aber sie zielen darauf ab, viel größere Objekte wie Stühle, Tische und Regale herzustellen.
In Zukunft könnten große Holzprodukte flach an einen Bestimmungsort verschifft und dann vom Kunden zu Hause getrocknet werden, um die endgültige Form zu erhalten.
Als flaches Rechteck gedruckte Holztinte wird so programmiert, dass sie nach dem Trocknen und Erstarren eine komplexe Form (z. B. eine Helix, abgebildet) bildet

Abgebildet ist die gedruckte Holztinte, bevor sie getrocknet wurde. Es ist bereits bekannt, dass Pflanzenmaterial beim Trocknen seine Form oder Textur verändern kann
Die Kreation könnte eines Tages das Ende des Zusammenbaus von Flat-Pack-Möbeln wie von IKEA bedeuten – für viele aufgrund der körperlichen Anstrengung und der komplizierten Natur der Anweisungen ein Alptraum.
“Am Zielort könnte sich das Objekt in die gewünschte Struktur verziehen”, sagte Doktorand Doron Kam, einer der Schöpfer an der Hebräischen Universität Jerusalem.
Es ist bereits bekannt, dass Pflanzen ihre eigene Form oder Textur verändern können, nachdem sie gefällt wurden, und ihre Form ändern, wenn sie trocknen.
Wenn beispielsweise ein Baum gefällt wird, schrumpft er ungleichmäßig und verzieht sich aufgrund von Abweichungen in der Ausrichtung der Holzfasern.
„Verzerrung kann ein Hindernis sein, aber wir dachten, wir könnten versuchen, dieses Phänomen zu verstehen und es für eine wünschenswerte Verwandlung nutzbar zu machen“, sagte Kam.
Bereits 2019 stellte das Team seine umweltfreundliche Tinte auf Wasserbasis vor, die aus Mikropartikeln aus Holzabfällen, bekannt als „Holzmehl“, gemischt mit Zellulose-Nanokristallen und Xyloglucan (natürlichen Bindemitteln, die aus Pflanzen gewonnen werden) besteht.
Die Forscher druckten die Holztinte mit einem 3D-Drucker, der mithilfe von Software ein bestimmtes Design erstellt, bevor er von Robotergeräten gedruckt wird.
Automatisierte Roboterarme haben am Ende eine Düse, die die Drucksubstanz – in diesem Fall Holzpartikel – Schicht für Schicht ausstößt.
Das Team hat nun gezeigt, dass die Art und Weise, wie die Tinte aufgetragen wird, oder der „Pfad“, das Morphing-Verhalten beim Verdunsten der Feuchtigkeit bestimmt.
Beispielsweise trocknet und schrumpft eine flache Scheibe, die als eine Reihe konzentrischer Kreise gedruckt ist, und bildet eine sattelartige Struktur, die an ein Pringles-Crisp erinnert – von Mathematikern als „hyperbolisches Paraboloid“ bekannt.
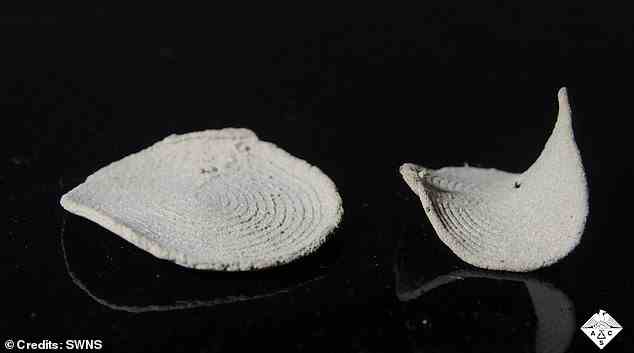
Eine flache Scheibe, die als eine Reihe konzentrischer Kreise gedruckt ist, trocknet und schrumpft, um eine sattelartige Struktur zu bilden, die an ein Pringles-Crisp erinnert – von Mathematikern als „hyperbolisches Paraboloid“ bekannt.

Bereits 2019 stellte das Team seine umweltfreundliche Tinte auf Wasserbasis vor, die aus Mikropartikeln aus Holzabfällen besteht, die als „Holzmehl“ bekannt sind (im Bild), gemischt mit Zellulose-Nanokristallen und Xyloglucan (natürliche Bindemittel, die aus Pflanzen gewonnen werden).
In der Zwischenzeit verwandelt sich eine Scheibe, die als eine Reihe von Strahlen gedruckt ist, die von einem zentralen Punkt ausgehen, in eine Kuppel oder eine kegelartige Struktur.
Und das Stapeln von zwei rechteckigen Schichten, die in unterschiedlichen Ausrichtungen gedruckt werden, ergibt nach dem Trocknen eine Helix.
Die endgültige Form des Objekts nach dem Trocknen kann auch durch Anpassen der Druckgeschwindigkeit gesteuert werden, fand das Team heraus.
Wie schnell die Holztinte aufgetragen wird, verändert den Grad der Ausrichtung der Fasern in der Tinte und folglich das Verziehen, wenn sie trocknet
Bei einer langsameren Druckgeschwindigkeit sind die Partikel zufälliger ausgerichtet, sodass eine Schrumpfung in alle Richtungen auftritt. Unterdessen richtet schnelleres Drucken die Fasern aneinander aus, sodass sich die Schrumpfung stärker auf einen Bereich konzentriert.
Eine weitere Verfeinerung wird es dem Team ermöglichen, Kuppeln, Spiralen und andere Designmotive in einem einzigen Objekt zu kombinieren – eines, das viel größer ist als das, was sie demonstriert haben.
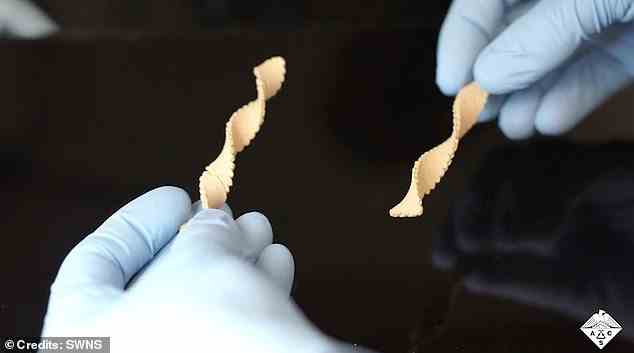
Eine weitere Verfeinerung wird es dem Team ermöglichen, Kuppeln, Spiralen und andere Designmotive in einem einzigen Objekt zu kombinieren – eines, das viel größer ist als das, was sie demonstriert haben

Für viele ist das Zusammenbauen von Flat-Pack-Möbeln von IKEA aufgrund der körperlichen Anstrengung und der komplizierten Anleitung ein Alptraum
Schließlich könnte es möglich sein, die Technologie für den Heimgebrauch zu lizenzieren, damit Verbraucher ihre eigenen Holzobjekte mit einem normalen 3D-Drucker entwerfen und drucken können.
Solche Verbraucher würden jedoch Zugang zu einer Art Vorrichtung benötigen, die solche Objekte trocknen könnte – die möglicherweise mehrere Fuß lang sein könnten. MailOnline hat die Forscher gefragt, was das sein könnte.
Das Team untersucht auch, ob der Morphing-Prozess unter bestimmten Bedingungen reversibel gemacht werden könnte, sodass das Hartholz wieder zur Weichholztinte werden könnte.
Dies würde möglicherweise eine Ära einläuten, in der Verbraucher ihre Holzmöbel kontinuierlich recyceln und sie jederzeit in neue Formen umwandeln können.
„Wir hoffen zu zeigen, dass wir diese Elemente unter bestimmten Bedingungen reagieren lassen können – zum Beispiel auf Feuchtigkeit – wenn wir die Form eines Objekts wieder ändern wollen“, sagte Eran Sharon von der Hebräischen Universität Jerusalem.
Das Team wird seine Technik auf dem Treffen der American Chemical Society (ACS) vorstellen, das diese Woche virtuell und persönlich stattfindet.