Apple attaches great importance to the durability of its products. And with “Daisy” he has nevertheless developed a robot that wants to destroy her particularly effectively. That was a bigger challenge than expected.
It’s the beginning of the end of an iPhone. He begins with a grabbing motion, a quick grab. A white arm grabs the device from the assembly line. A jerky movement brings it over an opening, after a critical examination by the camera below it is transported with another quick swing into a holder. Another arm grabs hold of the iPhone 6s with the lower end in a device – and separates the display from the housing with a nimble lever. After that, the two go their separate ways.
The arm belongs to Daisy, Apple’s first smart recycling robot. Daisy is standing in an inconspicuous factory building on a closed-off site in Breda, Netherlands, separating the wheat from the chaff for Apple, or the resources from the e-waste.
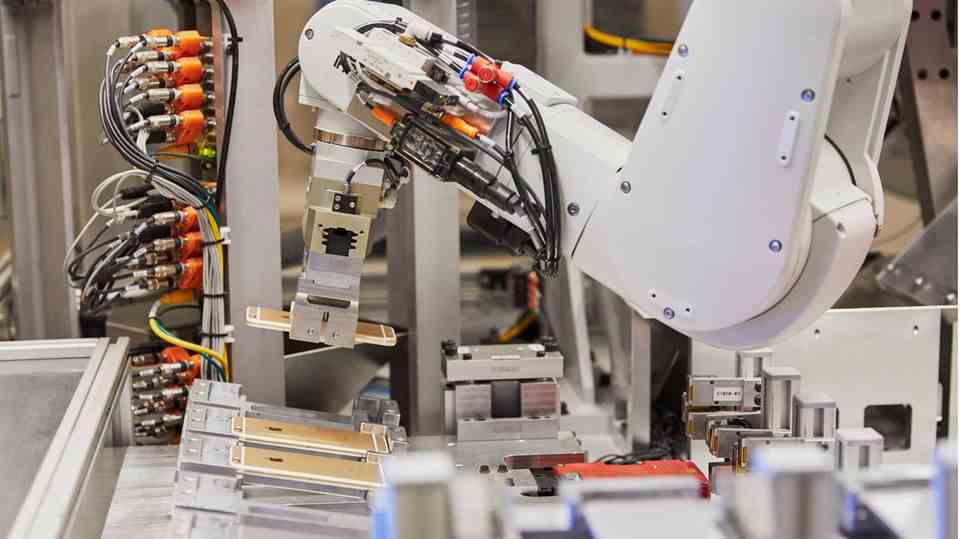
Apple’s recycling robot Daisy disassembles iPhones into their individual parts in several steps
© Apple / PR
Apple is rethinking
The recycling efforts are part of a rethink within the group. For a long time, like the rest of the industry, the environmental impact of the tens of millions of devices manufactured each year was given too little thought. For several years now, Apple has been working very actively to reduce the company’s ecological footprint and at some point even turn it around. “We are well on the way to eventually being able to manufacture our products entirely without mining raw materials,” explains Lisa Jackson, the top manager responsible for environmental and political initiatives in the Group’s current environmental report.
This can be done in two ways. On the one hand, the group attaches great importance to the fact that reused raw materials are actually recycled material and has this confirmed by certificates. In addition, you take the recycling into your own hands with Daisy and two other recycling robots.
Recycle smarter
Much simpler methods still prevail in the recycling industry. Many recycling companies simply shred the devices to get them into a more manageable size. The big advantage: from laptops to smartwatches, many different products can be dismantled by the same machine. However, this has its price. Because the machines work very roughly, many components such as the sensitive magnets are damaged when they are dismantled, and they literally crumble to dust if handled roughly. This means that valuable resources are almost irretrievably lost: rare earths are found in the magnets. Other recycling approaches, such as automated small hammering or screening drums, also did not offer the degree of sensitivity that Apple desired. So they came up with the idea of developing a robot for it.
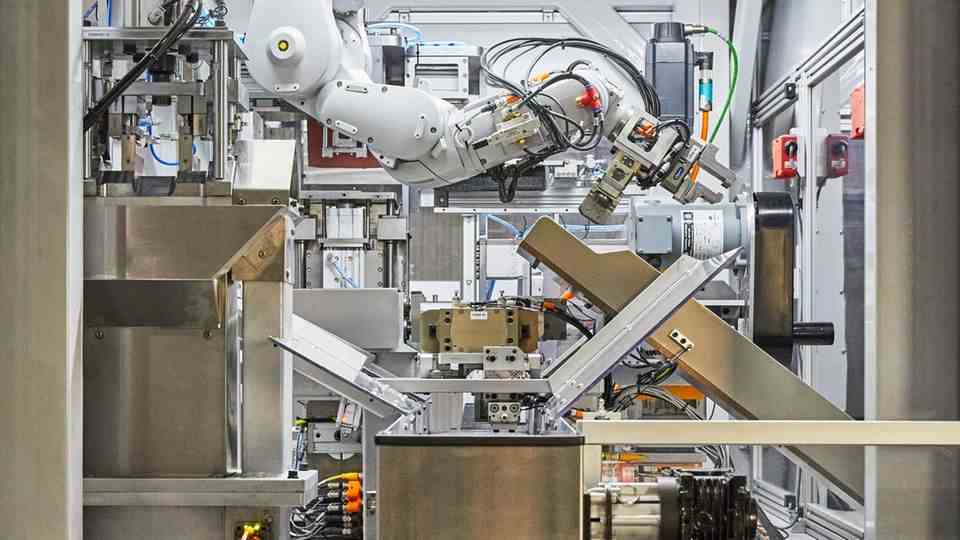
Daisy is spread over several boxes, in each of which different work steps take place
© Apple / PR
The way to Daisy was quite long. Its first predecessor, called Liam 1.0, was developed back in 2014. He still needed a full twelve minutes to disassemble a single iPhone. The successor, who developed Liam 2.0 almost a year later, only needed 11 seconds. Daisy now needs 18 seconds – but unlike the two Liam models, she can no longer disassemble just a single iPhone model, but 23 different ones, from four variants of the iPhone 13 to the iPhone 5 released in 2012.
Punching instead of screwing
You had to completely rethink, reports an Apple engineer. Apple had previously perfected the assembly of the devices in its production facilities, suddenly the exact opposite was the goal with the disassembly. While at the beginning of the recycling experiments the assembly was basically played out in reverse, this quickly turned out to be impractical.
This has consequences: The first Liam also took so long because he carefully took each screw out of the housing. Daisy’s approach is far less timid today: with a fast-moving rod, she simply punches the screws one after the other through the motherboard, much like a hole punch. And is done with it after about three seconds. After all, when it comes to recycling, it doesn’t matter whether the screw holes are still usable. Entire components such as the Taptic engine, which is responsible for vibration, are now simply punched out. You can follow the disassembly in detail in the video above.
When the robot is done with the work, the iPhones end up neatly broken down into workable parts in baskets that are slowly filling with housings, camera units or motherboards. It may be the end for the individual device, its raw materials will find new life in a new device.
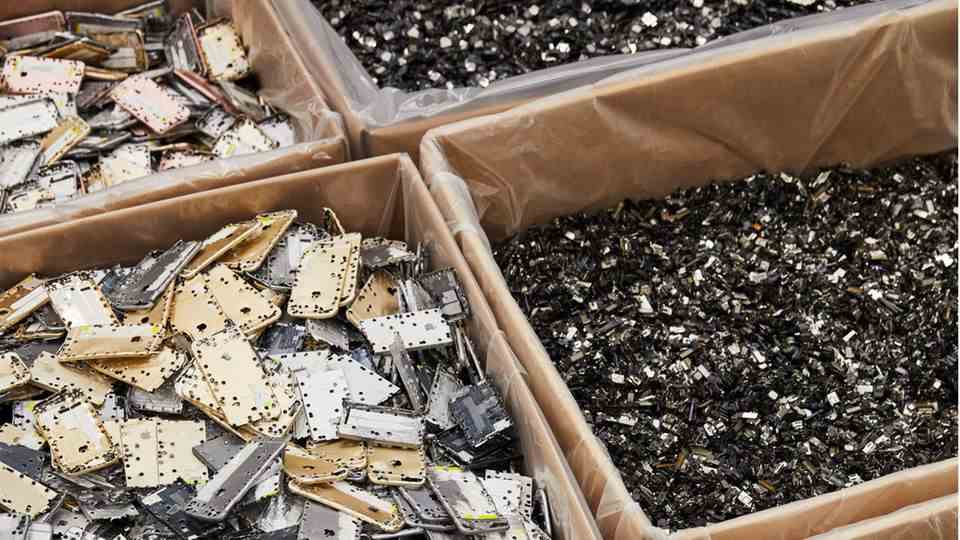
The items are collected in baskets. The camera units are on the right, for example, and the aluminum housing is on the left
© Apple / PR
Recycled is not the same as recycled
Despite the relatively rough approach, Daisy is much gentler than any shredder. Because the Taptic engine, the speakers with their magnets brimming with rare earths, or the camera with its high gold and copper content remain in one piece, the valuable resources can be recovered from them more reliably than from the mishmash of fragments created by a shredder full of plastic, aluminum and precious metals.
At the same time, another problem of conventional recycling processes is avoided: the contamination of the material caused by the mixing. This is extremely important for Apple. Because the group attaches great importance to the extremely high quality of the materials used in the manufacture of its products, the use of recycled raw materials is a particularly great challenge. It’s easy to “downcycle” an iPad case and make a beverage can out of it, for example. But if you want to produce high-quality and just as stable new devices from recycled materials, you have to put a lot more work into the recycling and avoid contamination from plastic residues or other metals.
But that’s exactly Apple’s long-term goal. The group is already very successful with aluminum, as the annual environmental report shows. Whether it’s the Apple Watch Series 7, the current notebooks from the Macbook Air or Macbook Pro series, or the newly introduced iPad Air: the majority of the Apple devices introduced last year are made from 100 percent recycled aluminum . Apple also achieves similar rates in some components for gold or the rare earths used in speaker magnets. For the 14 most important materials, Apple has a confirmed recycling rate of 18 percent, and the group wants to increase it further.
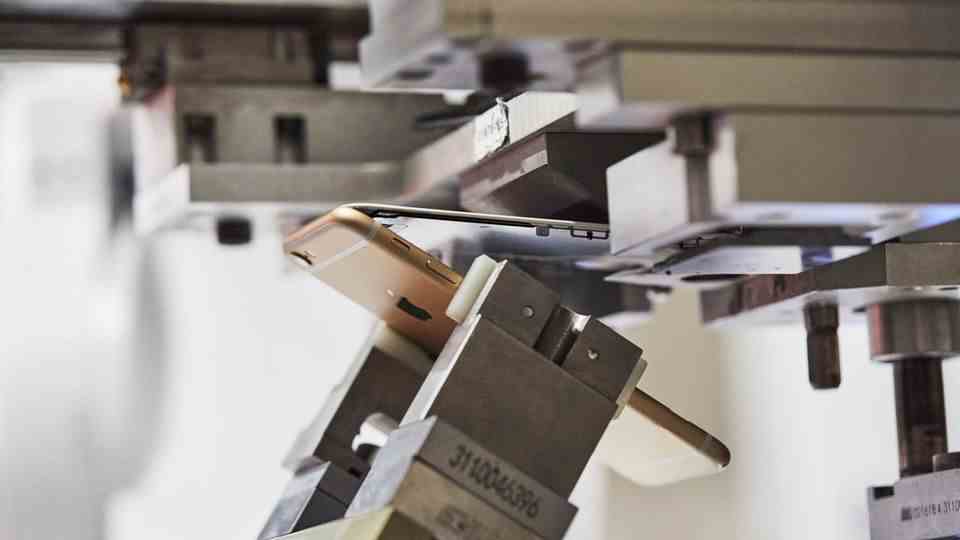
When disassembling, Apple’s robot is quite rough
©Apple
Long lifetime
If Apple has its way, recycling is just the last step. The group has been trying for a long time to increase the service life of individual devices with ever more stable housings, long-term support with new software versions, cheaper battery replacement and a program for self-repair of numerous devices
According to the motto “Better in use than in the drawer” Apple also buys up old devices for this purpose. If possible, the refurbished devices are then offered to customers again; However, if the devices that have been handed in are too old or damaged, Apple only accepts them for disposal free of charge – and feeds them to Daisy.
Great plans
Apple is far from where the company wants to be. However, it is on the right track in its efforts to become more sustainable. By 2030, the group wants to work completely climate-neutral. “We’ve already done that for our own business,” Jackson emphasizes. The operation of the company headquarters in Cupertino and the work of the employees are completely balanced by environmental projects, Apple explains, and the work is also virtually waste-free. When it comes to the manufacture of the devices and their components, Apple is also on track to make them climate-neutral. “Today, 213 of our suppliers have committed to running all Apple jobs using 100 percent renewable energy,” Jackson said. According to the group, this also has a signal effect: Many of the suppliers have also started to convert the rest of the production. A desired effect.
There is still room for improvement when it comes to recycling. Daisy could disassemble 1.2 million iPhones every year, just like her sister of the same name in Austin, Texas. The group does not want to reveal how many there actually are, but both recyclers still have free capacity until things get tight. One would like to recycle more devices, explains the engineer. But customers are currently making even less use of the group’s disposal offers than it would like. This is also the reason that so far only the iPhone – by far the group’s best-selling product – has been dismantled using the robot. Should the limit of 1.2 million devices be broken at some point, that would not be a real problem for the group: there would also be room for more Daisys in the warehouse in Breda.